AGMA’s Fall Technical Meeting is your gateway to gear and power transmission innovation.
MPT Expo attendees can also register to experience AGMA’s annual Fall Technical Meeting (FTM), an event that brings together top researchers from around the world to share their latest peer-reviewed gear industry research. Network with industry experts, academics, and engineers, ask your burning questions, and gain valuable insights into the future of the motion and power industry.
Important 2025 Update - New FTM Dates
We are pleased to announce that the 2025 Fall Technical Meeting will be held from Wednesday, October 22 through Friday, October 24.
To better accommodate your schedule and maximize the value of your time, we have adjusted the dates of this meeting, formerly held on Monday-Wednesday of the MPT Expo. Changing to a Wednesday-Friday schedule allows for:
• Less overlap with the main expo, providing more opportunity for attendees to attend both events.
• More networking opportunities with colleagues and industry peers on the show floor.
• A more streamlined and efficient event for both attendees and exhibitors.
Please mark your calendars for the new dates and sign up for show alerts below.
2025 FTM Agenda at a Glance
Wednesday, October 22
MPT What's Brewing Power Breakfast
8:00 am – 9:45 am
FTM Session 1 and Q&A
10:00 am – 1:00 pm
Awards Luncheon
1:00 pm – 2:15 pm
FTM Session 2 and Q&A
2:30 pm – 5:30 pm
Optional: MPT Networking Reception
Additional ticket required
7:00 pm – 10:00 pm
Thursday, October 23
MPT What's Brewing Power Breakfast
8:00 am – 9:45 am
FTM Session 3 and Q&A
10:00 am – 1:00 pm
Lunch on the show floor
1:00 pm – 2:15 pm
FTM Session 4 and Q&A
2:30 pm – 5:30 pm
FTM Networking Reception
6:30 pm – 8:30 pm
Friday, October 24
FTM Breakfast
8:00 am – 9:00 am
Session 5 and Q&A
9:00 am – 12:00 pm
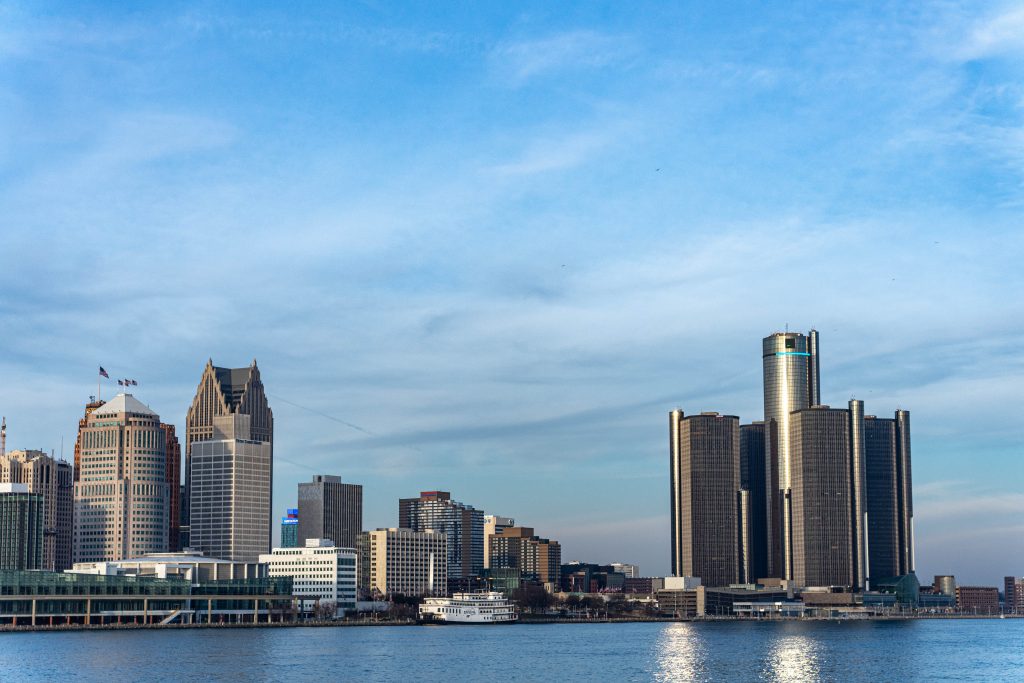
Super Saver May 15 – July 15 | Early Bird July 16 – September 16 | Advance September 17 – October 20 | Late October 20 – Onsite | |||||
---|---|---|---|---|---|---|---|---|
Member | Non-Member | Member | Non-Member | Member | Non-Member | Member | Non-Member | |
FTM: Full Pass*** Oct. 22-24 8am-5:30pm | $1,250 | $1,650 | $1,300 | $1,700 | $1,350 | $1,750 | $1,450 | $1,850 |
FTM Single Session: Session 1** Oct. 22 10am-1pm | $425 | $525 | $450 | $550 | $475 | $575 | $500 | $600 |
FTM Single Session: Session 2** Oct. 22 2:30-5:30pm | $425 | $525 | $450 | $550 | $475 | $575 | $500 | $600 |
FTM Single Session: Session 3** Oct. 23 10am-1pm | $425 | $525 | $450 | $550 | $475 | $575 | $500 | $600 |
FTM Single Session: Session 4** Oct. 23 2:30-5:30pm | $425 | $525 | $450 | $550 | $475 | $575 | $500 | $600 |
FTM Single Session: Session 5** Oct. 24 9am-12pm | $425 | $525 | $450 | $550 | $475 | $575 | $500 | $600 |
FTM: Speaker Pass*** Oct. 22-24 8am-5:30pm | $395 | $395 | $395 | $395 | $395 | $395 | $395 | $395 |
FTM: Student Pass*** Oct. 22-24 8am-5:30pm | $200 | $200 | $200 | $200 | $200 | $200 | $200 | $200 |
FTM: Professor Pass*** Oct. 22-24 8am-5:30pm | $450 | $450 | $450 | $450 | $450 | $450 | $450 | $450 |
FTM: Awards Luncheon Oct. 22 1-2:15pm | $65 | $80 | $75 | $90 | $85 | $100 | $95 | $110 |
FTM: Networking Reception Oct. 23 6:30-8:30pm | $80 | $95 | $90 | $105 | $100 | $115 | $110 | $125 |
*Included in registration
- Trade show floor access on October 21-23 including all show floor presentations
- Access to the Opening Night Welcome Reception on October 21 from 4pm – 6pm with two drink tickets
**Included in registration
- Complimentary Expo Pass which includes trade show floor access on October 21-23 including all show floor presentations and access to the Opening Night Welcome Reception on October 21 from 4pm – 6pm with two drink tickets
- Access to selected education course including materials and refreshments
***Included in registration
- Complimentary Expo Pass which includes trade show floor access on October 21-23 including all show floor presentations and access to the Opening Night Welcome Reception on October 21 from 4pm – 6pm with two drink tickets
- Access to selected education course including materials and refreshments
- Access to What's Brewing Breakfast and Sessions on 10/21-10/23 from 8am-10am
- Access to FTM Awards Luncheon on 10/22 and FTM Networking Reception on 10/23
Wednesday, October 24
Technical Session 1: Design and Rating
10:00 am – 1:00 pm
-
How Many Gears for Electric Cars? One Example
Dr. Bernd-Robert Höhn, Gear Research Center (FZG), Technical University of Munich -
Cross-Correlation of Design Variables for Epicyclic System
Dr. Claudio Autore, Ferrari S.p.A. -
Particle-Based CFD Study of Lubrication in Power Transmission Systems Using Local Refinement Techniques
Benjamin Legrady, Dive Solutions GmbH -
Modeling Lubricated Flow and Thermal Response for Gears
Dr. Weixue Tian, ExxonMobil Technology and Engineering Company
Technical Session 2: Electric Vehicles and Emerging Technology
2:30 pm – 5:30 pm
Thursday, October 25
Technical Session 3: Manufacturing and Inspection
10:00 am – 1:00 pm
-
Influence of Precipitation Conditions on the Tooth Root and Pitting Load Carrying Capacity of Carbonitrided and Low Pressure Carburized Gears
Niklas Blech, Gear Research Center (FZG), Technical University of Munich -
Methodology to Evaluate the Bending and Contact Allowable Stress Numbers of Gear from Rotating Bending Database
Dr. Luc Amar, CETIM -
Advanced Distortion Control for Case Hardening of Transmission Components
Dr. Volker Heuer, ALD Vacuum Technologies GmbH -
SPECIAL PRESENTATION: Updates to AGMA 926 – Recommended Practice for Carburized Aerospace Gearing
Scott Davidson, AGMA Aerospace Gearing Committee/Boeing Rotorcraft – Philadelphia
Technical Session 4: Efficiency and NVH
2:30 pm – 5:30 pm
-
Non-Linear Analysis of Gear-Fatigue-Damage Under Variable Load
Daniel Vietze, Gear Research Center (FZG), Technical University of Munich -
Use of Gear Reliability Data in a Cloud-Based Gearbox Digital Twin
Barry James, Hexagon -
Wear Behavior of Polymeric Compound Measured on a New Test Rig for Plastic Gears
Dr. Riccardo Longato, Longato Riccardo Srls -
Tooth Flank Fracture – Investigations on the Influence of Overloads on the Fatigue Strength of Case-Hardened Gears
Sascha Rommel, Gear Research Center (FZG), Technical University of Munich -
Experimental and Analytical Study of the Effect of Shot Peening on Gear Micropitting and Contact Fatigue Failure
Dr. Dalia Jbily, CETIM
Friday, October 26
Technical Session 5: Materials and Performance
9:00 am – 12:00 pm
-
Laser Material Processing for the Production of Bronze Coatings for Tribological Applications
Dr. Hannes Freisse, Kugler Bimetal SA -
Influence of Tooth Root Contour Deviations on the Tooth Bending Strength
Christian Eggert, Laboratory for Machine Tools and Production Engineering (WZL), RWTH Aachen University -
Power Skiving Tool Offsets and the Feasibility of Using a Calculator for Manipulating the Resulting Geometry
Bethany Cousins, The University of Sheffield Advanced Manufacturing and Research Centre (AMRC) -
Virtual End of Line Test – Prediction of the Acoustic Behavior of Gearboxes Based on Topographic Deviations Using Neural Networks
Marius Willecke, Laboratory for Machine Tools and Production Engineering (WZL) of RWTH Aachen University
Advance Member (ends Oct. 4) |
Advance Nonmember (ends Oct. 4) |
Late Member (ends onsite) |
Late Nonmember (ends onsite) |
|
---|---|---|---|---|
Full Pass | $1,350 | $1,650 | $1,450 | $1,750 |
Single Sessions | $400 | $500 | $425 | $525 |
Student Pass | $200 | $200 | $250 | $250 |
Professor Pass | $450 | $450 | $500 | $500 |